Tests, inspection and certification of playground areas
The management of safety in playgrounds is an ongoing process, interactive between all the agents involved and responsible for playgrounds and sports areas, systematic because it requires procedures, and dynamic because they are constantly being used.
The safety assessment of the product, its inspection and certification within play areas, playgrounds and sports areas are all included within the management process and they are fundamental to maintaining these areas in the same conditions as when the design and installation plan for the space was first carried out.
Safety management implies a task that all agents involved in the process, from public or private administrators to workers, teachers, carers, instructors, etc., must carry out to keep playgrounds and sports spaces safe.
Hence the importance of an independent and certified body such as ourselves carrying out the corresponding inspections and certifications of playgrounds, as well as auditing the maintenance management process of the areas themselves.
However, to be able to inspect and certify said spaces it is vital to always start with safe products that have been assessed by a testing laboratory which guarantees that the manufactured product complies with European and international standards, and to then inspect the facilities and finally, to assess them make annually to verify their safety.
We are the only entity accredited by ENAC to perform laboratory or in situ tests, and we are an inspection body under the umbrella of Regulations ISO EN 17025 and ISO EN 17020. With more than 30 years’ experience in child safety, we have technical knowledge and experience in all matters involving children, both insofar as products and environments are concerned. Requirements ranging from child development, design requisites, installation, maintenance and usability.
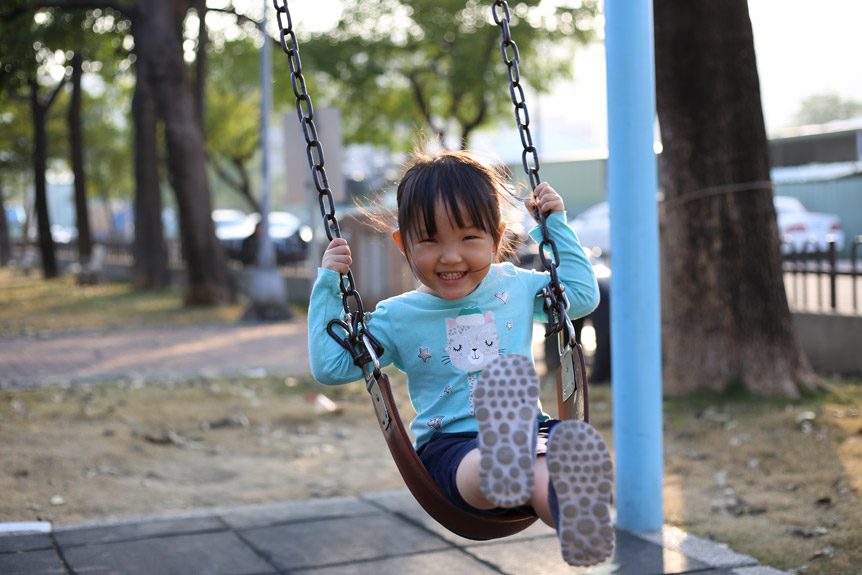
Services involved in tests, inspection and certification in playgrounds
The annual inspection and certification of playgrounds, as recommended by standard EN 1176-7 “Playground Equipment and Surfacing. Part 7: Guidance on Installation, Inspection, Maintenance and Use”. We inspect both playground equipment and surfacing, and all ancillary items located in recreational area.
All sports equipment must be annually assessed due to the use made of it, mainly in those places where children and teenagers can play and practice sports freely or under supervision, given that they are more vulnerable in the case of any sports equipment falling over, such as a basketball ring or a goal.
By being able to routinely and annually inspect how training equipment located in outdoor fitness areas work, and by carrying out adequate management thereof, it is possible to avoid risks and important incidents caused by their use and their close location to play areas.
Having inflatable playequipment adequately designed according to current regulations, ensuring they are correctly installed and annually inspected in order to determine whether such equipment still retains the safety properties it originally had, mainly due to the inflation of the equipment, would mean that children could play on and use this equipment without any unforeseeable risk of injuries or serious accidents, because said risks are not evident and children are not aware of them while they play on them.
This type of place, apart from complying with building legislation, must also comply with the safety requirements established in their specific European technical regulation, which encompasses and covers specific aspects for this structures of this nature, such as exit and evacuation routes, visibility, the possibility of being able to climb on the exterior, containment walls/nets in relation to the safety area, its resistance to ignition, ball pool requirements, signage, etc.
Using technical regulation EN 1176 part 1 as our tool, we assess the safety of such furniture. Our knowledge in safety assessment, fundamental to avoid unacceptable risks in such items as fences, is the most basic example we can find in our spaces. It is fundamental to perform a risk assessment in order to assess their safety.
Having certified playing recreational areas and playgrounds is part of an inspection process that provides a guarantee of safety in areas in which children spend most of their time. The fact that we can offer this service implies that an external entity has verified the facilities, which in turn provides added value and a recognition of the management system enforced by those responsible for the playground, be that a public or private Administration, the manufacturers, maintenance companies, restaurants, schools, property managers, etc., They can all ensure that they are offering their most vulnerable audience a “safe” playing space.
Playground and recreation equipment, as is the case with other products placed on the market, must be safe and it is up to the manufacturers, through recognised test laboratories, to demonstrate that their product is safe, albeit through the existence of a specific regulation. All products on the market must comply with European Directive on the General Safety of Products 1801/2003, which applies to all European Union member states and is transposed at a national level, and ensures that the user receives a product that is safe.
Those responsible for placing inflatable play equipment on the market, i.e., the manufacturers, must guarantee and preserve the safety and health of users. For all these reasons, it is essential that such equipment undergoes the pertinent tests, has the necessary documents for its installation, inspection and maintenance, and the labelling that such inflatable play equipment must have, in a visible place on the inflatable castle or flat-bed, prior to it being used. Test laboratories have the authority to perform these tests, offering the buyer of the inflatable play equipment a greater guarantee, greater control over production, as well as revising the toxicity of the ornamental materials used for the design of the different inflatable equipment.
It is very important to carry out the pertinent tests on these products to assess their safety, whether once they have been installed or at the factory. We check whether fixed training equipment already installed prior to the publication of the new EN 16630 standard can be adapted and whether newly manufactured equipment is safe.
All surfaces are suitable for children’s playgrounds and outdoor fitness areas, but it is the maximum fall height of the different playground and fitness equipment that will determine what type of surface is required and how much impact it must be able to absorb.
Therefore it is very important to perform laboratory tests that allow us to identify the critical fall height for an HIC of 1000 (Head Injury Criteria) that the surface presents before installation, or to perform these tests “in situ”, mainly on those surfaces installed “in situ”, in order to determine the level of cushioning it provides within the impact area of each playground equipment permanently installed outdoor fitness equipment.
All sports equipment, goals, baskets, etc. must be assessed in the factory, in accordance with their current European regulations, and once they have been installed in the different sports areas before use. This is because any product placed on the market must be safe, and those responsible must be able to guarantee its safety during its entire useful life, which includes inspections and appropriate maintenance, in order to ensure its usability.
We are a Technological Centre specialising in child safety and product quality; we provide our clients with our markings and certifications, offering them a tool which will allow the end consumer to distinguish their product from that of the competition, and to be confident that they are buying a well-made article, with guarantees of safety and quality.
Consumer and public demand for children’s products with safety and quality guarantees is increasing.
That is why at AIJU we provide our customers with our certifications and seals like a tool that allows the end user to distinguish your product from those of the competition, and to offer them the confidence that they are buying an article with safety and quality guarantees.
The “SEGURIDAD CONTROLADA” (controlled safety) mark for children’s products allows end users to differentiate the products that have such a mark from those of the competition, not only in terms of safety, but also of quality, because in addition to European Union safety requirements, at AIJU we request additional requisites depending on the product. We also carry out an annual follow-up which guarantees the uniform level of quality of these articles.
What are the advantages?
- It makes your product stand out from others by the competition, increasing its credibility, safety and image in the market.
- It defines the quality of the product, based on objective criteria: safety regulations, technical specifications and additional quality requirements.
- It guarantees a uniform level of product safety on a continuous basis.
- It generates a prestige that guarantees a high safety level for the manufacturer’s products, checked and certified by a recognised and competent body.
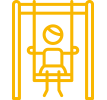


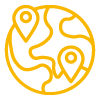
The fact that the manufacturer of and those responsible for the playground guarantee that it complies with applicable technical regulations, and they fact that they can guarantee that they are assessed and inspected during their entire lifetime by independent organisms accredited by ENAC is a member of ILAC, as we are, benefit, in the first instance, the end consumer, because they are using adequate and safe equipment and facilities, and in the second instance, those responsible themselves, reducing costs and unforeseeable accidents
As a testing laboratory, we assess the safety of both playground and sports equipment as well as surfaces as follows:
- Physical and chemical tests and design checking, in accordance with national and European regulations, etc.
- Assessment of the information or instructions for “safe” use during its entire lifetime (installation, inspection, maintenance).
- Revision of the marking in order to guarantee traceability if a dangerous risk were to arise.
All this benefits the manufacturer by complying with European General Product Safety Directive 1801/2003, which applies to all European Union member states and is transposed at a national level, and ensures that the user receives a product that is safe.
Test reports obtained in our laboratory are internationally recognised, because they are performed in Europe, in an accredited and certified laboratory.
On the other hand, we are an inspection body:
- We inspect the recreational area and/or facilities, playground and sports equipment, and playing surfaces installed in situ, in accordance with the requirements of the European standard.
- We draw up technical assessment rulings, in order to be able to check the safety of playgrounds.
- We audit the state of maintenance of the recreational area and its management.
The technical staff and inspectors who perform the tests and inspections of playground and sports equipment and surfaces have over 10 years’ experience in the sector. Being an active member of different standardization committees, both national and European, entails the ongoing training of the personnel involved, offering the customer all possible updates of the standards in order to have the most up-to-date products on the market. This generates the necessary confidence in our customers.
We are an active member of several national and international standard-setting forums and committees related to child safety.
At the national level:
- CTN 172/SC 03 “Playgrounds”
- CTN 147/SC 02 “Sports, Playing Fields and Other Recreation Equipment”
At the European level, within the CEN/TC 136/SC1 “Playground Equipment for Children”:
Groups in which we take part or have taken part as an expert member:
- TG1 “Rationale”, whose mission is to prepare a document that interprets the different requirements of the family of play area standards.
- WG 1 “Surfacing”, in which studies are being carried out to add new requirements to Regulation EN 1177.
- WG 13 “Playground Equipment and Surfacing”. This group is in charge of revising the general part of Regulation EN 1176-1.
- WG 14 “Revision of EN 1176 Parts 2, 3, 4, 5 and 6”. This group is in charge of revising the group of regulations for playing equipment.
- “Interpretation panel”; a group of experts there to answer questions about the interpretation of regulations, the most frequent doubts manufacturers have, test laboratories, inspectors, consumers, etc.
- TG 2 “The Competence of Playground Equipment Inspectors”; a group in charge of determining the competence of inspectors to achieve a unification of criteria and assessments.
- WG 12 “Play of All”; created due to the existing problem regarding the access of children with disabilities to playground and playground equipment.
- WG 26 “Outdoor Adult Fitness Equipment”; a group of experts responsible for drawing up standards for outdoor sports equipment used by children due to its proximity to playgrounds.
- WG9 “Inflatable play equipment”; a group of experts responsible for modifying Regulation EN 14960, the technical standard for inflatable play equipment, and for creating new parts that encompass requirements and test methods for other types of inflatable game equipment.
